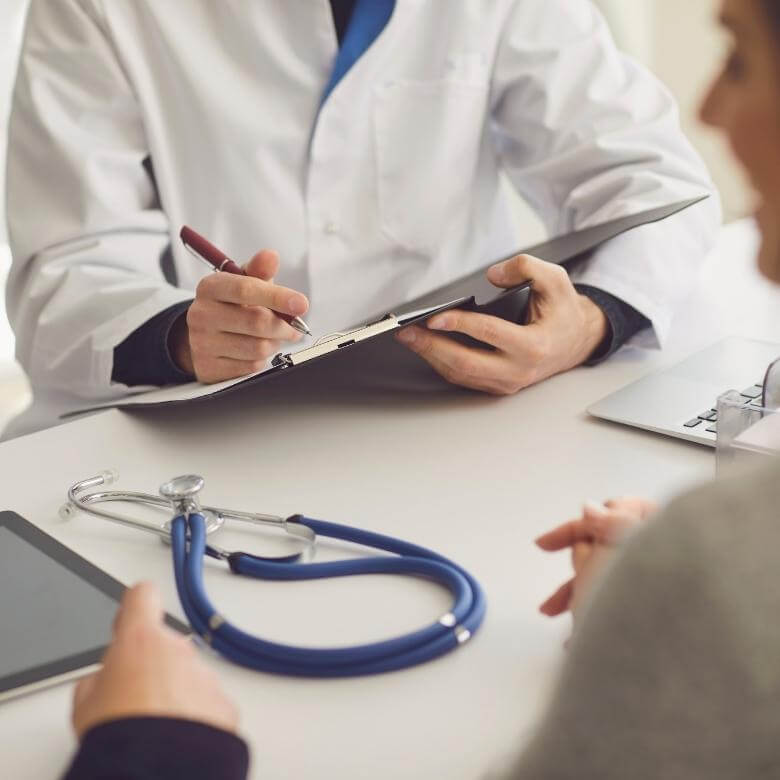
ISO 13485: Medical Devices Quality Management System (MDQMS)
In July of 2003, the ISO 13485 quality management system standard for businesses operating in the medical device industry was first introduced by the International Organization for Standardization (ISO). On March 1, 2016, the latest version of ISO 13485:2016—which took the place of ISO 13485:2003—was published.
ISO 13485:2016 is a rule that concentrates on how a corporation could handle a risk-based approach related to the purchase, production, storage, design and development, installation, distribution, and servicing activities, and other facets of the quality management system. It is built on the same fundamental ideas and clause schema as ISO 9001:2015. The standard outlines standards for businesses involved in one or more phases of the life cycle of a medical device. It is frequently seen as an essential first step in ensuring design and manufacturing processes continually result in high-quality goods that satisfy regulatory standards.
Objective Of ISO 13485
ISO 13485 may also be used by importers or appointed distributors that ship in and issue medical devices and may be needed to set up a quality management system under local regulations.
The primary objective of ISO 13485:2016 is to hasten the harmonisation of quality management system regulatory standards for medical devices. Because of this, it contains particular standards for medical equipment and leaves out some of the ISO 9001 requirements that are unsuitable for regulatory criteria. Due to these exemptions, organisations that have achieved ISO 13485 certification cannot assert that their quality management systems are under ISO 9001 unless they do so.
Benefits of Obtaining ISO 13485 Certification
in Malaysia
Who Needs Certification of ISO 13485 in Malaysia?
ISO 13485 certification is essential for any organisation in Malaysia involved in the design, production, installation, and servicing of medical devices.
Elevate your team's expertise with bespoke ISO training—contact our ISO training providers in Malaysia for tailored solutions. To find out how to obtain ISO 13485 certification, you may refer to our article for the procedures.
Medical Device Manufacturers
Companies that produce medical devices, equipment, or instruments need certification to ensure their products meet global quality and safety standards.
Suppliers and Distributors
Businesses supplying components or distributing medical devices can benefit from ISO 13485 certification to demonstrate compliance and gain trust with manufacturers and end-users.
Healthcare Facilities
Hospitals, clinics, and labs that handle medical devices should consider certification to ensure proper management and maintenance of equipment.
Contract Service Providers
Firms offering services like sterilisation, packaging, or quality control for medical devices must comply with ISO 13485 to meet client and regulatory requirements.
Top Six Reasons to Adopt ISO 13485 for Your Business
The Process of Achieving Certification of ISO 13485 in Malaysia
Achieving ISO 13485 certification in Malaysia involves a structured process to ensure your organization meets all the required standards for medical device quality management. Here’s an overview of the steps involved:
Initial Consultation
The first step is to schedule a consultation with One Island Consultancy. During this meeting, we assess your organization's current quality management practices and identify any gaps that need to be addressed.Gap Analysis
Our team conducts a thorough gap analysis to evaluate your existing processes against ISO 13485 Malaysia requirements. We will highlight areas for improvement and help you develop an action plan.Document Preparation and Implementation
The next step is to prepare and implement the necessary documentation required by ISO 13485. This includes procedures for design control, production, risk management, and traceability.Employee Training
We provide specialized training for your employees on ISO 13485 standards and best practices. This ensures that your team is well-equipped to maintain and improve the quality management system.Internal and External Audits
Once the system is in place, we perform internal audits to ensure compliance with ISO 13485. External audits are conducted by a third-party certification body to verify that your system meets all required standards.Certification
After successful audits, your organization will receive ISO 13485 certification in Malaysia, demonstrating that your processes meet international quality management standards.Ongoing Support and Surveillance
Post-certification, we offer ongoing support to ensure your company remains compliant. Regular surveillance audits are essential to maintain your certification and continuous improvement.
ISO 13485 Malaysia: Empowering Excellence in Medical Device Quality Management Training
At One Island Consultancy, we offer specialised ISO 13485 Malaysia training to help organisations in the medical device industry meet the stringent requirements of this international standard. Our training equips your team with the knowledge and skills to establish, implement, and maintain an effective Quality Management System (QMS) for medical devices.
Who Should Attend the Training of ISO 13485 Malaysia?
Our ISO 13485 Malaysia training is designed for professionals involved in quality management and medical device manufacturing, including:
- Quality Managers and Quality Assurance Teams
- Regulatory Affairs Specialists
- Top Management and Decision Makers
- Medical Device Designers and Engineers
- Internal Auditors
Why Choose ISO 13485 Malaysia Training with Us?
- Industry-Focused Curriculum: Tailored for organisations in Malaysia’s medical device sector, our training ensures compliance with both ISO 13485 and local regulatory requirements.
- Expert Guidance: Learn from experienced trainers with in-depth expertise in ISO 13485 implementation and auditing.
- Practical Insights: Gain hands-on knowledge through real-world examples and case studies that prepare your team to address industry challenges.
- Customized Approach: Whether you’re new to ISO 13485 or looking to enhance your existing QMS, our training is adaptable to your organisation’s specific needs.
Benefits of ISO 13485 Malaysia Training
- Ensure compliance with international and local medical device regulations.
- Build a robust Quality Management System to enhance product safety and performance.
- Improve your organisation’s credibility and access to global markets.
- Minimise risks and non-conformities in the manufacturing process.
Take the first step toward achieving ISO 13485 certification in Malaysia. Contact us today to learn more about our training programs and how they can help your organisation excel in the medical device industry.
Why Choose Us for ISO 13485 in Malaysia
At One Island Consultancy, we are committed to helping businesses in the medical device industry achieve ISO 13485 Malaysia certification with expert guidance and tailored solutions. Here’s why we are the best choice for your ISO 13485 certification journey:
Expert Knowledge and Experience
With years of experience in ISO 13485 Malaysia, our team has a deep understanding of the medical device industry’s unique requirements. We offer expert advice, ensuring your company meets the highest standards of product safety, quality, and regulatory compliance.
Tailored Solutions for Your Business
We understand that every business is unique. That's why we offer customized solutions that are specifically designed to meet your organization's needs. Whether you're a large manufacturer or a small medical device producer, we create an implementation plan that fits your requirements.
Proven Track Record of Success
Our proven track record speaks for itself. We've successfully guided numerous businesses through the ISO 13485 certification process, helping them achieve compliance with international standards and enhancing their product quality management systems.
Comprehensive Support at Every Step
From initial consultation to certification and beyond, we provide full support throughout the process. We help with every step—gap analysis, documentation preparation, internal audits, employee training, and more—ensuring your company is well-equipped to maintain compliance.
Cost-Effective Solutions
We offer cost-effective solutions that align with your budget and resources. Our goal is to help you achieve ISO 13485 certification efficiently, without unnecessary costs or delays. We focus on providing value by streamlining the process and ensuring lasting results.
Ongoing Assistance and Continuous Improvement
We don't just help you achieve ISO 13485 Malaysia certification; we also provide continuous support to ensure your quality management system remains compliant and effective. Our team is always available for refresher training, surveillance audits, and any other needs you may have after certification.
Explore More ISO Certification Options in Malaysia
At One Island Consultancy, we specialise in guiding businesses to achieve international standards across various industries. Whether it’s environmental management, food safety, or information security, we offer tailored solutions to meet your specific needs. Explore our range of ISO certifications:
Case Studies: Certification of ISO 13485 in Malaysia
Explore how One Island Consultancy has helped various organizations in Malaysia achieve ISO 13485 certification. These case studies showcase the challenges businesses faced, the solutions provided, and the successful outcomes after implementing a Quality Management System (QMS) for medical devices.
Case Study 1: Medical Device Manufacturer X – Expanding Market Reach
Industry: Medical Device Manufacturing
Challenge:
Medical Device Manufacturer X, based in Malaysia, was experiencing growth but faced challenges in meeting international regulatory standards. They wanted to improve their internal processes to align with global best practices and gain entry into more competitive international markets.
Solution:
One Island Consultancy assisted Medical Device Manufacturer X in adopting ISO 13485 Malaysia. We guided them through the entire process, from gap analysis to full implementation of their QMS. The focus was on improving design control, risk management processes, and ensuring all product lifecycle stages, from production to distribution, met regulatory standards. Additionally, we provided training tailored to their operational needs to ensure everyone understood their responsibilities under the new system.
Outcome:
Medical Device Manufacturer X successfully achieved ISO 13485 certification in Malaysia and immediately began accessing international markets. The certification enhanced their credibility, boosted customer trust, and streamlined their production processes, leading to greater efficiency and reduced compliance risks.
Case Study 2: Company Y – Quality Assurance for Healthcare Services
Industry: Healthcare Services
Challenge:
Company Y, a healthcare service provider, needed to ensure that the medical devices used in their operations met stringent regulatory requirements. They sought ISO 13485 certification in Malaysia to improve their management of healthcare equipment and enhance service quality.
Solution:
One Island Consultancy worked with Company Y to implement ISO 13485 as part of their QMS for healthcare equipment management. We conducted a thorough audit of their existing procedures and identified areas for improvement. Our team developed a customized strategy for implementing quality control processes, ensuring that medical equipment handling, maintenance, and servicing adhered to ISO 13485 Malaysia standards.
Outcome:
After implementing ISO 13485 Malaysia, Company Y improved the quality control of medical devices, ensuring higher safety and reliability in healthcare services. The certification helped them align with industry standards and enhanced their reputation among patients and stakeholders.
Case Study 1: Medical Device Manufacturer X – Expanding Market Reach
Industry: Medical Device Manufacturing
Challenge:
Medical Device Manufacturer X, based in Malaysia, was experiencing growth but faced challenges in meeting international regulatory standards. They wanted to improve their internal processes to align with global best practices and gain entry into more competitive international markets.
Solution:
One Island Consultancy assisted Medical Device Manufacturer X in adopting ISO 13485 Malaysia. We guided them through the entire process, from gap analysis to full implementation of their QMS. The focus was on improving design control, risk management processes, and ensuring all product lifecycle stages, from production to distribution, met regulatory standards. Additionally, we provided training tailored to their operational needs to ensure everyone understood their responsibilities under the new system.
Outcome:
Medical Device Manufacturer X successfully achieved ISO 13485 certification in Malaysia and immediately began accessing international markets. The certification enhanced their credibility, boosted customer trust, and streamlined their production processes, leading to greater efficiency and reduced compliance risks.